Sub-Micron Purification
Why Sub-micron Purification Matters
Sub-micron purification was never a goal in the past because there has never been an effective method to perform it. Therefore, industry stopped at 3 micron filtration. Unfortunately, for mission critical equipment, 3-microns is simply not efficient in removal of the hardest and most damaging contamination. These particles form varnish, sludge, and cause significant wear.
Sub-micron purification as a goal is possible today because there is a solution. ISOPur® is the first company to deliver an effective, cost-efficient sub-micron purification solution. ISOPur Balanced Charge Agglomeration® effectively removes nearly all contaminants greater than 0.1 micron in size. ISOPur removes particle contamination; ferrous and non-ferrous wear debris, products of oxidation, and bacterial/biological contamination. ISOPur BCA® is an order of magnitude improvement over the finest mechanical filters.
The Misconceptions
This may seem like a reasonable question. After all, most conventional filtration systems are content with filtering particles to the 10 micron level – the big boulders that can grind, pit, and dent components.
Moreover, the ISO standard codes for measuring fluid cleanliness have three numbers – a 4-micron, a 6-micron, and a 14-micron measurement.
In truth, the reason why the ISO standard measures to 4 microns is because most full flow mechanical filteration simply isn’t able to remove particles smaller than 3 microns. While it is possible to make finer filters (e.g. going to one-micron filters), it is impractical. A one-micron filter builds up substantial back pressure, plugging the system. If the filter doesn’t fail, it rapidly plugs from contamination and requires frequent and expensive changeouts. Additionally a fine filter with high flow can cause problems through static discharge. Another reason that ISO codes stop at 4-microns is because it is difficult to measure particle counts at the 3-micron size without some highly advanced and costly instrumentation.
Tolerances of Critical Components
In order to understand whether purification at the sub-micron level matters, it is important to understand the components that lubrication is designed to protect. Components such as bearings, gears, pumps, pistons, valves, etc. operate at extremely high speeds, temperatures, and pressures. They also operate at very low tolerances. The following chart shows the typical thickness of the lubricating fluid in several common components:
As the above table shows large, mission critical machinery runs on slivers of oil that frequently run into the micron and sub-micron range.
The Concentration of Destructive Small Particles
We now know that the tolerances in these components is extremely small. Now let’s take a look at the typical composition of oil contamination (graphs provided by Noria Corporation):
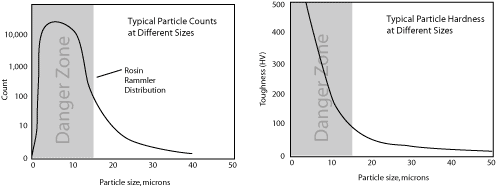
These curves reveal two things:
- The disproportional concentration of contaminants in the 0.1 to 5 micron range. In fact over 50% of contamination occurs in this range.
- The disproportional hardness of these 0.1 to 5 micron particles.
If we now marry the facts about component clearances to the facts about the prevalence of small destructive particles, it means that traditional mechanical filtration fails to remove the vast majority of the destructive particles circulating through high-performance machinery.
Component | Clearance (microns*) | |
---|---|---|
Roller Element Bearings | 0.1-3 | |
Journal Bearings | 0.5-100 | |
Gears | 0.1-1 | |
Engines | Ring/Cylinder | 0.3-7 |
Rod Bearing | 0.5-20 | |
Main Bearings | 0.8-50 | |
Piston Pin Bushing | 0.5-15 | |
Valve Train | 0.0-1.0 | |
Gearing | 0.0-1.5 | |
Pump, Gear | Tooth to Side Plate | 0.5-5 |
Tooth Tip to Case | 0.5-5 | |
Pump, Vane | Vane Sides | 5-13 |
Vane Tip | 0.5-1 | |
Pump, Piston | Piston to Bore | 5-40 |
Valve Plate to Cylinder | 0.5-5 | |
Servo Valves | Orifice | 130-450 |
Flapper Wall | 18-63 | |
Spool to Sleeve | 1-4 | |
Actuators | 50-250 |